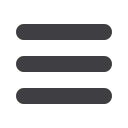
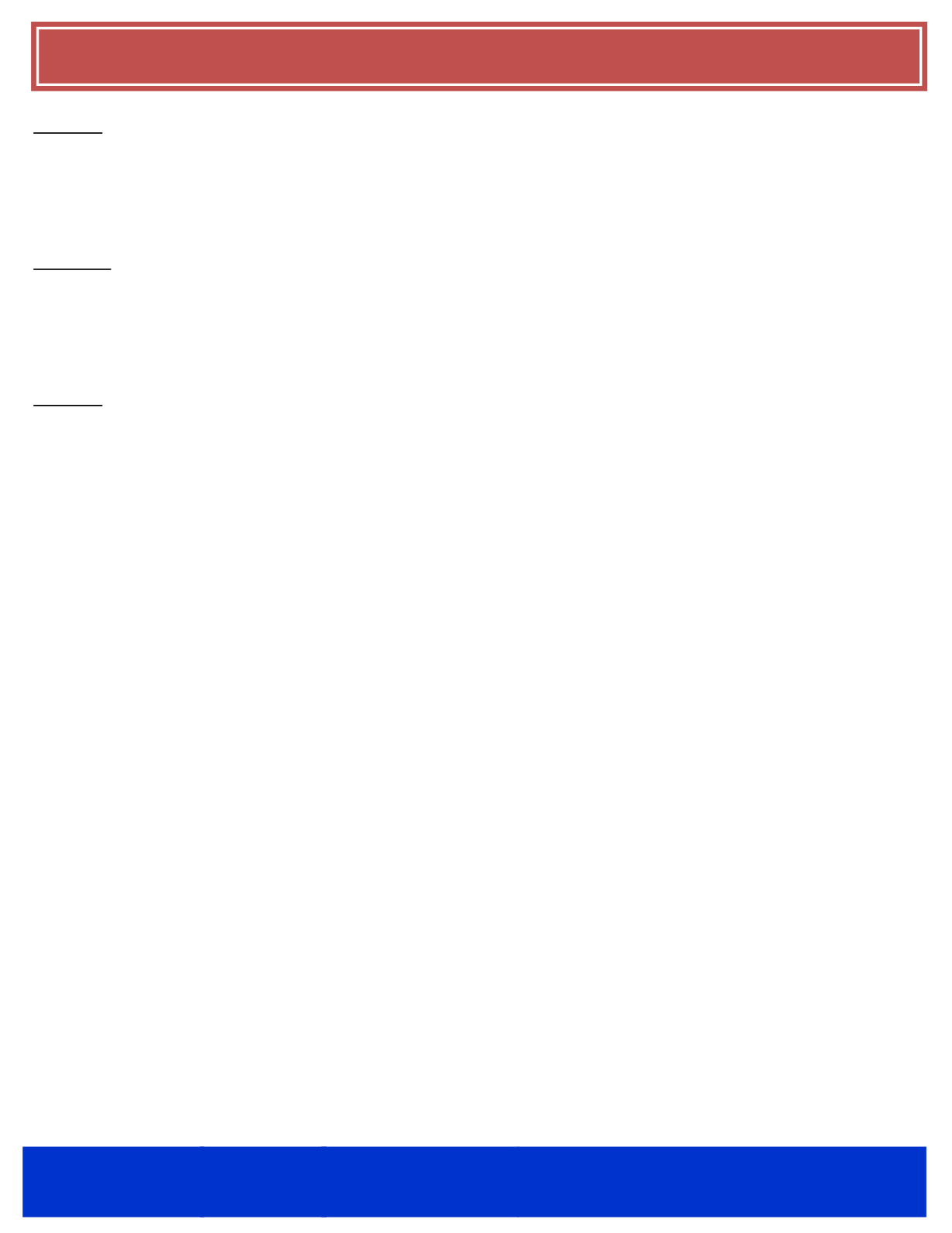
Marlin NanoLube
™
marlinnanolube.comCUSTOMERS CHALLENGE'S / NANOLUBE™ SOLUTIONS
Customer Challenge:
A Manufacturing Company’s main rotary compressor shut down by high limit temperature alarm.
NANOLUBE Solution:
After adding Transmission & Gear Box Supplement to the compressor it ran within limits. After some 40hrs of operation shut
down by internal high pressure limit. The compressor had never before been capable of developing the pressure and capacity
so pressure control was set high for max output. After high limit pressure repair, controls set to 130 psi and compressor easi-
ly cycled and delivered capacity. Also ran quieter.
Customer Challenge:
A leading cement plant experienced a major failure on their trunnion bearing. The trunnion bearing shaft was badly cut. To
change-out the trunnion would require several unscheduled days. They took a chance in changing out only the failed bearing,
leaving the scored trunnion which weights approximately 50 tons in place.
NANOLUBE Solution:
They added Transmission & Gear Box Supplement to the high pressure lube system. The trunnion bearing lasted until sched-
uled outage. The bearing under the scored shaft did not have a mark on it.
They also switched to High-Temp Lithium Complex Grease, and reported a 30 (400 lbs) drums savings from the previous year
with a competitor grease.
Customer Challenge:
A Rock Quarry company was experiencing problems with their out board bearing on a manual clutch on a large 600 horse-
power crusher. The bearings problems that occurred were costing the company between $10,000 + in parts and labor, plus
2-4 days of down time on the crusher.
NANOLUBE Solution:
After adding Transmission & Gear Box Supplement to their equipment they reported: ..”we have not experienced any more
problems with the bearing failure.”
Customer Challenge:
A small oil producer in Kansas was having problems with the gear boxes on their pump jacks.
NANOLUBE Solution:
After adding Transmission & Gear Box Supplement to the gear boxes, they reported the following on 5 pump jacks: 16% re-
duction in amps, 35% reduction in amps, 7% reduction in amps, 8% reduction in amps, and 10% reduction in amps.
Customer Challenge:
A nationally known grocers-retailer warehouse operated 20 Crown Reach-Forks and 35 Crown Pallet Jacks. They were expe-
riencing an alarming bearing failure rate on Reach-Forks averaging 87 per month at an average of $17.00 per bearing; Pallet
Jack failures averaged 17 per month at an average of $14.00 per bearing.
NANOLUBE Solution:
They switched to High-Temp Lithium Complex Grease, and have reported a $20,000 savings on bearing and a substantial
amount on maintenance man hours. They also reported grease consumption was roughly half that of their former grease.
Customer/Challenge:
A custom fabrication operation required two forming reductions with heat treatment and 10% scrap.
NANOLUBE/Solution:
Using Multi-Purpose on the piece and the dies the process was done in one operation with no HT and no scrap.
Customer/Challenge:
A major aircraft manufacture had reported high scrap problems on the aluminum skins (while being stretched) used on a
fighter plane.
NANOLUBE/Solution:
Metalform 2000 (a concentrate) was added to their existing metal form fluid. The orange peel problem no longer existed, and
they could pull and stretch more parts without having to coat every part. They approved Metalform 2000 (a finished product)
to be used in this application.
Customer/Challenge:
A machine shop that does mostly government work, was having problems on their horizontal milling machine, milling 1½” x
3” slots, and used 5 milling cutters which cost approx. $75. each.
NANOLUBE/Solution:
They used Industrial Super Lube on the next job, and only used 3 milling cutters to do the same job. A savings of $150.00
Customer/Challenge:
An Automotive manufacture was experiencing high cost on a Broaching Machine.
NANOLUBE/Solution:
They added machining fluid to their existing coolant, extended the regrind interval on a trial new broach from 500 parts to
2,500 parts. This saves on broach and regrind costs and provides longer uninterrupted production .
Customer/Challenge:
A major Aerospace company was having problems in milling five exotic aerospace material; QAJ Nickel, EAK St. Steel, 611C
Corrodible Steel, TAF Titanium, & INCO (901).
NANOLUBE/Solution:
They added Nanolube machining lubicant to their existing coolant. They reported the following: A 22.22% wear reduction, a
9.18% wear reduction, A 0.01% wear increase, A 22.20% wear reduction, A 18.98% wear reduction.
Customer/Challenge:
A company running industrial wire braiders experience continual wear and repair.
NANOLUBE/Solution:
They applied nanolube products and experienced a 7% reduction in amp readings. Also ran much quieter.